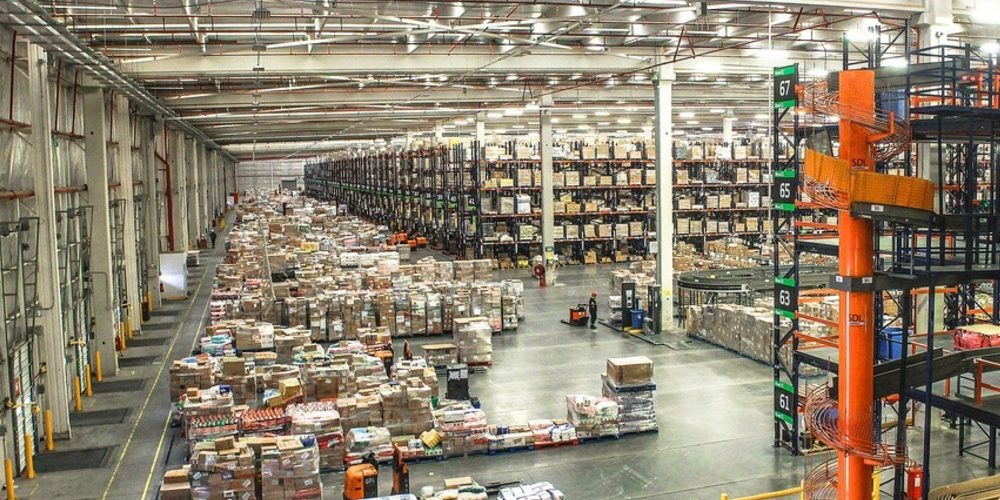
Situation
Our Client, who owns 75 shops in 44 cities throughout Romania and a dynamically growing online shop, has encountered a problem with their impractical central warehouse.
The central warehouse was limited in functionality due to outdated building layout and poor processes which were not suited to the current range of goods flowing through the DC. The picking places were dynamic, which led to several picking locations for one SKU.
The KPI’s were not properly adjusted, and the warehouse was overfilled.
Task
The client expected an appropriate location of the fastest-rotating products, maintaining an appropriate warehouse stock.
Improved storage processes are meant to prevent congestion in the picking aisles and its slow picking process. KPIs are to be properly adjusted to reflect key warehouse parameters.
Actions
- The warehouse processes were comprehensively audited
- The client’s logistics costs were benchmarked
- A wide range of improvement initiatives was identified
- The WMS system was selected
- Warehouse processes were consolidated and streamlined
- A new warehouse was selected and contracted
Results
- EUR 200 000 p.a OpEx reduction
- 100% All stock under one roof
- 20% Reduction of costs generated by warehouse transfers
By being involved in developing the new warehouse model, the different company functions understood their activities and interdependencies between them. This enabled major improvement within a short and long term storage strategy while also adjusting goals and KPI’s.
Project Info
- Service: Warehouse Design and Optimization
- Client: Major retailer in Romania
- Geography: Romania
Our Role
- Subject matter expertise
- Support with business case preparation
- Support in the process of moving processes to a new warehouse
- Support in exit from existing multiple buffer locations
- Support with HR selection
- Overall Programme Management
- Being part of SteerCo